Not known Details About Indonesia Furniture Manufacturers
Not known Details About Indonesia Furniture Manufacturers
Blog Article
5 Easy Facts About Indonesia Furniture Manufacturers Explained
Table of ContentsThe Only Guide for Indonesia Furniture ManufacturersSome Known Incorrect Statements About Indonesia Furniture Manufacturers Getting My Indonesia Furniture Manufacturers To WorkThe Ultimate Guide To Indonesia Furniture ManufacturersThe Definitive Guide to Indonesia Furniture Manufacturers
There are some disadvantages to getting from a furnishings manufacturer. For one, you may have to wait longer to get your furnishings because it's being tailored. In addition, you might not be able to see or touch the product prior to you get it. A furniture merchant is a business that markets furnishings made by various producers.When you buy from a furniture merchant, you're getting a piece of furniture that's currently been made and prepares to be shipped to your home. One of the benefits of buying from a furnishings store is that you can frequently see and touch the product prior to you acquire it.
At BH Furnishings, our team believe in setting brand-new requirements for excellence in the manufacturing of industrial furniture - Indonesia furniture manufacturers. Our dedication to technology has led us to embrace cutting-edge automation technology, changing the method we produce furniture and propelling us to the center of the sector. Gone are the days of hands-on labor dominating the production floor
State farewell to manufacturing hold-ups and overtime prices. This suggests we not just fulfill yet exceed delivery due dates, supplying our customers with a degree of integrity that typical manufacturing methods simply can't match.
The Single Strategy To Use For Indonesia Furniture Manufacturers
Our manufacturing ability has actually risen, permitting us to satisfy the needs of also the largest projects without jeopardizing on top quality. As your companion in industrial furniture remedies, we can easily scale our result to accommodate your requirements, despite the range. While standard production relies heavily on manual work, our automated systems have considerably minimized our dependancy on a large workforce.
Furniture production is a complicated process that involves numerous stages, from designing and product choice to manufacturing and assembly. At each phase, there is a possibility of defects or mistakes that can compromise the top quality of the end product. To make sure that furniture is of excellent quality, furniture suppliers execute quality assurance procedures to identify and remedy any concerns that may emerge during manufacturing.
The assessment process must cover various elements, such as assembly, coating, colour, design, product packaging, labelling, and marking. By applying an extensive inspection procedure, makers can ensure their products fulfill the necessary high quality, safety, and durability requirements. They likewise provide the versatility to resolve concerns and make improvements prior to finishing the end product.
Furnishings high quality criteria are collections of standards and demands for furnishings production. They define the needed top quality degree of furnishings manufacturing and cover elements such as security, toughness, stamina, and ecological effect.
The smart Trick of Indonesia Furniture Manufacturers That Nobody is Discussing

To guarantee their furnishings items can endure different weather condition elements, including sun, rain, snow, and wind, makers should take into consideration worldwide identified criteria that consist of examinations and screening. Below are a few of the standards to remember: ASTM F1561-03 is a global conventional developed by the American Section of the International Organization for Screening Materials (ASTM).
UL 962 is an international safety standard established by Underwriters Laboratories (UL), an independent worldwide supply security remedies firm. The standard applies to household and commercial furnishings, including outdoor furniture.
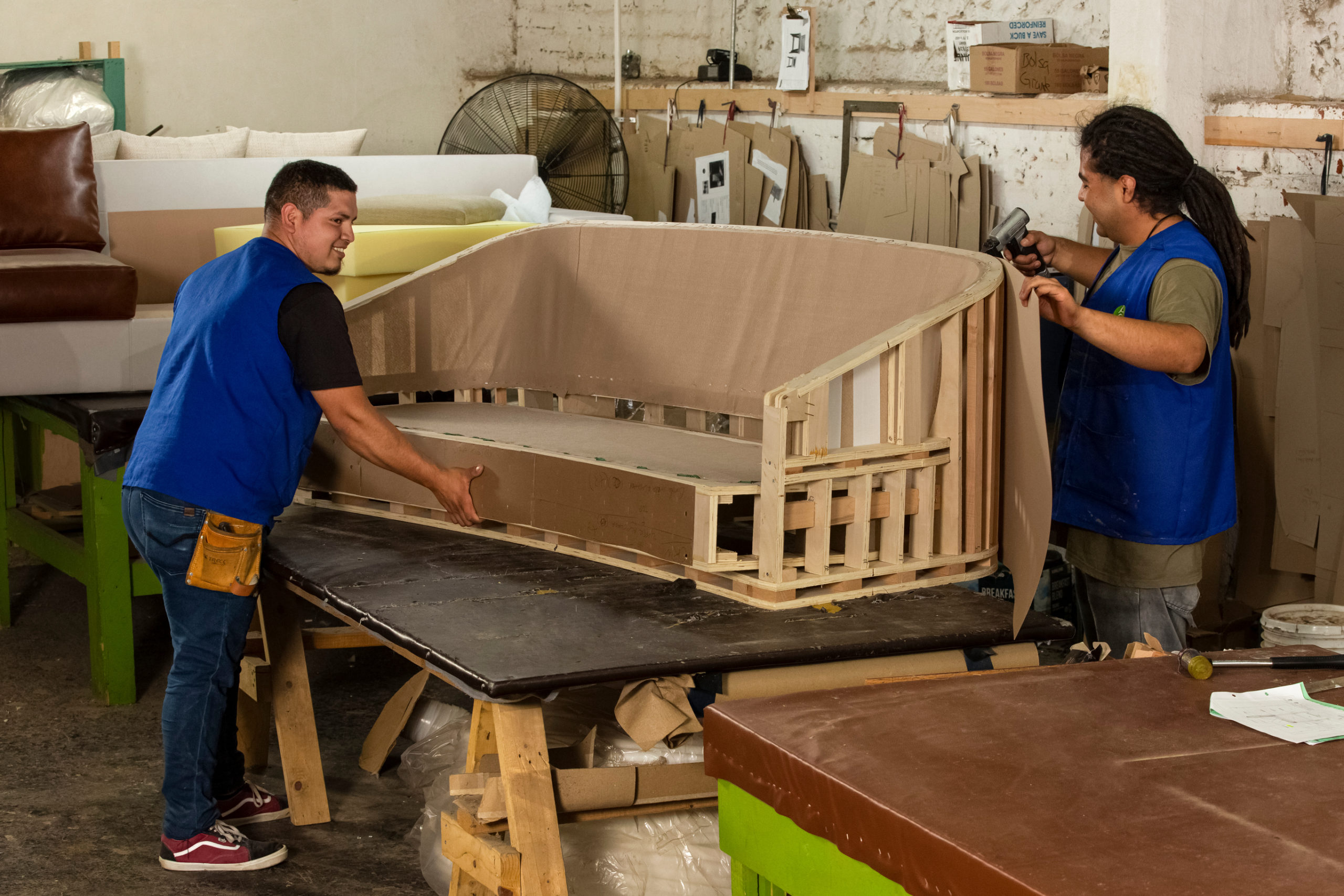
Little Known Questions About Indonesia Furniture Manufacturers.
It assists to determine issues in the furnishings and Your Domain Name evaluate its performance and compliance with the required high quality criteria. Below are the steps for carrying out lab testing for furnishings: Makers accumulate samples of furniture elements that need screening. These samples commonly stand for the various kinds of furnishings that they generate.
This may involve a mix of various examinations, including strength testing, sturdiness testing, safety testing, and ecological impact screening. The samples are then tested for numerous top quality specifications, such as stamina, resilience, safety, and ecological influence. The results are then reviewed to establish whether the products meet the called for top quality requirements.
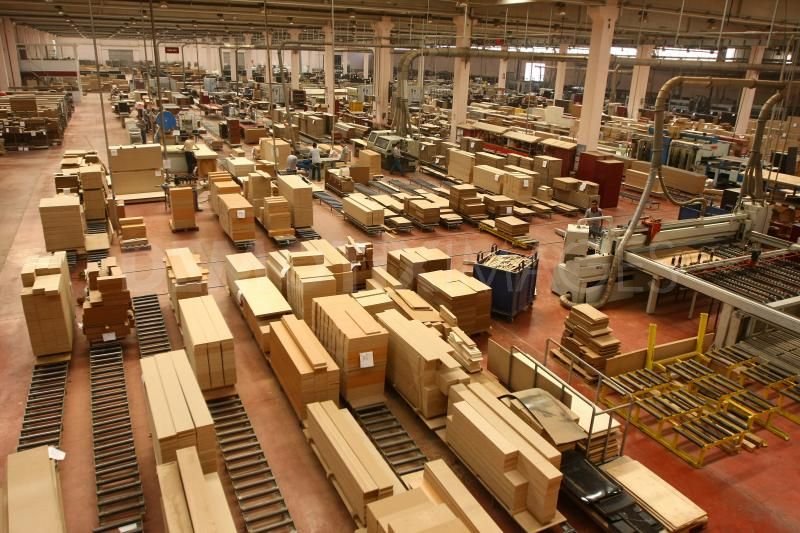
Typically, every retail store furniture is various. But all jobs have concerning a month's time between style ideation and last manufacturing. This is where the significant obstacle lies. Layouts meeting client convenience Optimizing space usage in storage, screen, step, visitor seats and walkways Guaranteeing simplicity of accessibility to items for tests and acquisition Designing modular furniture that is easy to move and refit Meeting security discover this info here requirements of consumers A fast TAT from layout to production and setup with marginal mistakes can assist attend to the above worries.
Facts About Indonesia Furniture Manufacturers Revealed
A designer can understand the market patterns and be all set with cutting-edge designs ahead of time. Review below: Just How DriveWorks Helps You to Reduce Preparation in Production Designers frequently need to change the forms and dimensions of furniture at a minute's notification. These may have various visual and practical needs like front desk, and servicing workdesk that vary in dimensions.
Improves item quality and lowers scrap. Field guideline files along with quantity departures are additionally produced for retail store furniture installments. Design models and conflicts are minimized, and the shop floor can begin manufacturing on the day of sales.
It is a very competitive market, with companies making every effort to keep up with altering customer needs and the newest technical fads. check this Today's consumers are extra most likely to favor furniture that is personalized and made with lasting products.
Report this page